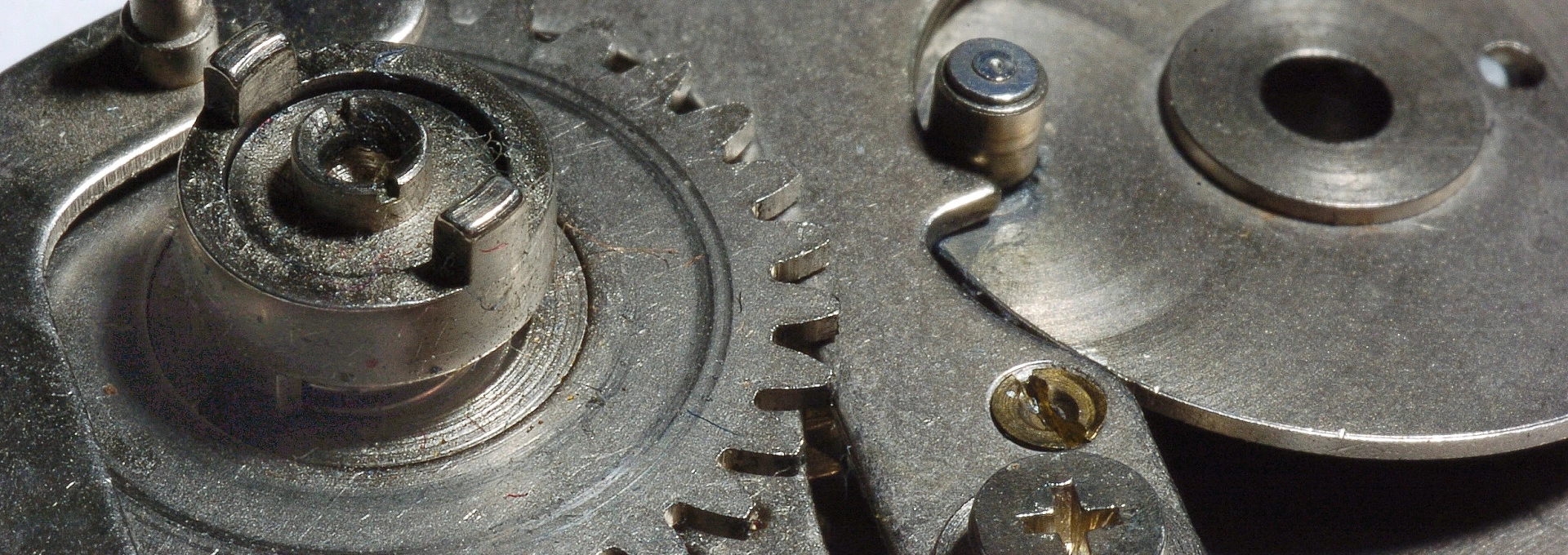
Les clavettes jouent un rôle fondamental dans l'assemblage et le fonctionnement des machines industrielles. Ces petites pièces mécaniques assurent la transmission du couple entre un arbre et un moyeu, tout en empêchant le glissement axial des éléments assemblés. Leur conception et leur dimensionnement précis garantissent une liaison solide et durable entre les composants rotatifs. Les clavettes se déclinent en plusieurs types adaptés à diverses applications, chacun présentant des caractéristiques spécifiques en termes de forme, de matériau et de tolérance. Une sélection judicieuse de la clavette appropriée, basée sur les contraintes mécaniques et l'environnement d'utilisation, s'avère déterminante pour optimiser les performances et la longévité des équipements industriels. Pour plus d'informations sur les différents modèles disponibles, vous pouvez consulter cette page.
Types de clavettes couramment utilisées en industrie
L'industrie mécanique emploie différents types de clavettes, chacun conçu pour répondre à des besoins spécifiques d'assemblage et de transmission de puissance. Les principaux modèles se distinguent par leur géométrie et leurs caractéristiques fonctionnelles, offrant des solutions adaptées à une large gamme d'applications. La compréhension des particularités de chaque type permet de sélectionner la clavette la plus appropriée pour garantir la fiabilité et l'efficacité des assemblages mécaniques.
Clavettes parallèles pour assemblages d'arbres cylindriques
Les clavettes parallèles, également appelées clavettes forme A selon la norme DIN 6885, constituent le type le plus répandu dans l'industrie mécanique. Leur forme rectangulaire simple facilite leur fabrication et leur mise en place. Ces clavettes s'insèrent dans des rainures usinées sur l'arbre et le moyeu, assurant une transmission efficace du couple. La symétrie de leur section transversale permet une répartition uniforme des contraintes, réduisant ainsi les risques de déformation ou de rupture sous charge. Les clavettes parallèles conviennent particulièrement aux assemblages d'arbres cylindriques soumis à des charges modérées à élevées. Leur longueur peut varier en fonction du couple à transmettre et du diamètre de l'arbre, offrant une flexibilité d'adaptation à diverses configurations mécaniques. La standardisation des dimensions des clavettes parallèles selon les normes internationales facilite leur approvisionnement et leur interchangeabilité, contribuant à la rationalisation des processus de maintenance industrielle.
Clavettes coniques pour fixations de moyeux
Les clavettes coniques se distinguent par leur profil trapézoïdal, offrant une surface de contact accrue entre l'arbre et le moyeu. Cette géométrie particulière permet une meilleure répartition des contraintes et facilite le démontage des assemblages, un avantage appréciable dans les opérations de maintenance. Les clavettes coniques s'avèrent particulièrement adaptées aux applications nécessitant une fixation solide du moyeu sur l'arbre, tout en permettant un ajustement précis de la position axiale. Leur forme conique génère un effet de coincement qui renforce la liaison mécanique, réduisant les risques de desserrage sous l'effet des vibrations. Cette caractéristique les rend particulièrement appropriées pour les équipements soumis à des chocs ou des variations de charge fréquentes. Néanmoins, l'usinage des rainures coniques requiert une précision accrue par rapport aux clavettes parallèles, ce qui peut influencer les coûts de fabrication et de maintenance des assemblages utilisant ce type de clavette.
Clavettes woodruff pour positionnements axiaux précis
Les clavettes Woodruff, reconnaissables à leur forme semi-circulaire, offrent une solution élégante pour les assemblages nécessitant un positionnement axial précis. Leur conception unique permet une insertion dans une rainure semi-circulaire usinée dans l'arbre, assurant ainsi un alignement parfait et une stabilité accrue de l'assemblage. Cette configuration réduit considérablement les risques de déplacement axial de la clavette, même sous des charges alternées ou des vibrations importantes. Les clavettes Woodruff s'avèrent particulièrement adaptées aux applications impliquant des changements fréquents de direction de rotation ou des inversions de couple. Leur faible hauteur minimise l'affaiblissement de la section de l'arbre, préservant ainsi sa résistance mécanique. Cependant, l'usinage spécifique requis pour les rainures Woodruff peut engendrer des coûts de fabrication plus élevés par rapport aux clavettes parallèles standard. Malgré cet inconvénient, les avantages en termes de précision et de stabilité justifient souvent leur utilisation dans des applications critiques, notamment dans l'industrie automobile et aérospatiale.
Dimensionnement optimal des clavettes selon l'application
Le dimensionnement adéquat des clavettes constitue une étape cruciale pour garantir la fiabilité et la longévité des assemblages mécaniques. Ce processus implique la prise en compte de multiples facteurs, tels que le couple à transmettre, les caractéristiques des matériaux utilisés, et les conditions d'exploitation de l'équipement. La détermination des dimensions optimales d'une clavette s'effectue généralement selon des normes établies, comme la DIN 6885 ou l'ISO 2491, qui fournissent des recommandations basées sur le diamètre de l'arbre et la puissance à transmettre. Le calcul du dimensionnement intègre plusieurs paramètres clés, dont la longueur de la clavette, sa largeur et sa hauteur. La longueur de la clavette influence directement sa capacité à transmettre le couple sans subir de déformation plastique ou de rupture par cisaillement. Cette dimension est généralement déterminée en fonction du couple maximal à transmettre et de la résistance au cisaillement du matériau de la clavette.
La largeur de la clavette, quant à elle, affecte la résistance au matage des surfaces en contact, tant sur l'arbre que sur le moyeu. Un choix judicieux de cette dimension permet de prévenir l'usure prématurée des rainures et d'assurer une répartition uniforme des contraintes. La hauteur de la clavette influence sa résistance au cisaillement et doit être choisie en tenant compte du diamètre de l'arbre pour maintenir un équilibre entre la résistance mécanique et la réduction de la section de l'arbre. Les ingénieurs utilisent souvent des facteurs de sécurité pour compenser les incertitudes liées aux conditions d'exploitation réelles, telles que les chocs, les vibrations ou les variations de charge. Ces facteurs permettent de surdimensionner légèrement les clavettes pour garantir une marge de sécurité suffisante sans compromettre l'efficacité globale de l'assemblage.
Le dimensionnement des clavettes doit également tenir compte des caractéristiques spécifiques de l'application, telles que la fréquence des démarrages et arrêts, les inversions de sens de rotation, ou encore l'exposition à des environnements corrosifs. Dans certains cas, l'utilisation de logiciels de calcul spécialisés ou de méthodes d'analyse par éléments finis permet d'affiner le dimensionnement en simulant le comportement de l'assemblage sous diverses conditions de charge. Cette approche analytique avancée s'avère particulièrement pertinente pour les applications critiques où la défaillance d'une clavette pourrait entraîner des conséquences graves en termes de sécurité ou de coûts opérationnels. L'optimisation du dimensionnement des clavettes contribue ainsi non seulement à la fiabilité des équipements industriels, mais également à leur efficacité énergétique en minimisant les pertes dues aux frottements et aux jeux mécaniques excessifs.
Matériaux constitutifs pour une résistance maximale
La sélection des matériaux constitutifs des clavettes détermine leurs performances mécaniques et leur durabilité dans diverses conditions d'utilisation. Les propriétés intrinsèques du matériau choisi influencent directement la capacité de la clavette à résister aux contraintes imposées par l'application, tout en assurant la longévité de l'assemblage. Cette sélection prend en compte de nombreux paramètres, notamment la résistance mécanique, la ductilité, la tenue en fatigue, et la compatibilité avec l'environnement opérationnel. Les concepteurs disposent d'une large gamme de matériaux pour répondre aux exigences spécifiques de chaque application, allant des aciers au carbone conventionnels aux alliages de haute performance.
Aciers alliés trempés pour les charges élevées
Les aciers alliés trempés se distinguent comme le choix privilégié pour les applications soumises à des charges élevées et des contraintes mécaniques intenses. Ces matériaux présentent une combinaison optimale de résistance mécanique et de ténacité, permettant aux clavettes de supporter des efforts de cisaillement et de compression considérables sans subir de déformation permanente. Parmi les nuances couramment utilisées pour la fabrication de clavettes, on trouve les aciers 4140, 4340 ou 8620, soumis à des traitements thermiques spécifiques visant à améliorer leurs propriétés mécaniques. Le processus de trempe et revenu génère une structure martensitique fine, conférant à la clavette une dureté élevée en surface tout en préservant un cœur tenace. Cette combinaison de caractéristiques assure une résistance accrue à l'usure et à la fatigue, prolongeant ainsi la durée de vie de l'assemblage mécanique.
La résistance mécanique supérieure des aciers alliés trempés permet l'utilisation de clavettes de dimensions plus réduites pour une même capacité de transmission de couple, contribuant à l'optimisation du rapport poids/performance des assemblages mécaniques. Cette caractéristique s'avère particulièrement avantageuse dans les secteurs où la réduction de masse constitue un enjeu majeur, comme l'industrie aéronautique ou automobile. De plus, la dureté élevée obtenue par le traitement thermique confère aux clavettes une excellente résistance à l'usure, réduisant ainsi les besoins en maintenance et les temps d'arrêt des équipements.
L'utilisation d'aciers alliés trempés pour la fabrication de clavettes nécessite une attention particulière lors des processus de fabrication et de montage. L'usinage de ces matériaux à haute résistance requiert des outils de coupe spécialisés et des paramètres d'usinage adaptés pour garantir la précision dimensionnelle et l'état de surface requis. De même, le montage des clavettes en acier allié trempé exige des précautions pour éviter tout endommagement des surfaces de contact, qui pourrait compromettre la performance de l'assemblage. La mise en œuvre de procédures de contrôle qualité rigoureuses, incluant des inspections dimensionnelles et des tests de dureté, s'avère indispensable pour assurer la conformité des clavettes aux spécifications techniques exigées.
Aciers inoxydables pour les environnements corrosifs
Dans les environnements sujets à la corrosion, tels que l'industrie chimique, agroalimentaire ou marine, l'utilisation d'aciers inoxydables pour la fabrication des clavettes s'impose comme une solution de choix. Les aciers inoxydables austénitiques, tels que les nuances 304 ou 316, offrent une excellente résistance à la corrosion grâce à la formation d'une couche passive d'oxyde de chrome en surface. Cette protection naturelle permet aux clavettes de conserver leurs propriétés mécaniques et dimensionnelles même en présence d'agents corrosifs, assurant ainsi la pérennité de l'assemblage mécanique. Outre leur résistance à la corrosion, les aciers inoxydables présentent également une bonne résistance mécanique et une ductilité appréciable, facilitant leur mise en forme et leur ajustement lors du montage.
Certaines nuances d'aciers inoxydables martensitiques, comme le 420 ou le 440C, peuvent être traitées thermiquement pour obtenir une dureté et une résistance à l'usure accrues, les rendant particulièrement adaptés aux applications combinant contraintes mécaniques élevées et environnement corrosif. Ces aciers offrent un compromis intéressant entre résistance mécanique et résistance à la corrosion, permettant leur utilisation dans des conditions opérationnelles particulièrement sévères. Toutefois, leur mise en œuvre nécessite une maîtrise approfondie des procédés de traitement thermique pour optimiser leurs propriétés sans compromettre leur résistance à la corrosion.
L'utilisation d'aciers inoxydables pour la fabrication de clavettes présente des avantages significatifs en termes de durabilité et de réduction des coûts de maintenance dans les environnements corrosifs. La résistance inhérente de ces matériaux aux attaques chimiques élimine la nécessité de traitements de surface supplémentaires, simplifiant ainsi les processus de fabrication et réduisant les risques de défaillance liés à la dégradation des revêtements protecteurs. De plus, la biocompatibilité de certaines nuances d'aciers inoxydables, telles que le 316L, élargit leur champ d'application aux secteurs médical et pharmaceutique, où les exigences en matière d'hygiène et de résistance à la stérilisation sont particulièrement strictes.
Alliages légers pour les applications aéronautiques spécifiques
Dans l'industrie aéronautique, où la réduction de masse constitue un enjeu primordial, l'utilisation d'alliages légers pour la fabrication de clavettes s'est imposée comme une solution technique avancée. Les alliages d'aluminium et de titane offrent un excellent rapport résistance/poids, permettant de concevoir des assemblages mécaniques performants tout en minimisant la masse totale des structures aéronautiques. Ces matériaux présentent des caractéristiques mécaniques adaptées aux contraintes spécifiques du domaine aérospatial, telles que la résistance à la fatigue, la tenue aux basses températures et la compatibilité avec les traitements de surface anticorrosion.
Les alliages d'aluminium de la série 7000, notamment le 7075-T6, se distinguent par leur résistance mécanique élevée et leur usinabilité. Ces propriétés en font des candidats de choix pour la fabrication de clavettes destinées aux assemblages d'arbres et de moyeux dans les structures secondaires des aéronefs. Le traitement thermique T6 confère à l'alliage 7075 une résistance à la traction pouvant atteindre 572 MPa, associée à une limite d'élasticité de 503 MPa. Cette combinaison de propriétés permet de concevoir des clavettes capables de transmettre des couples importants tout en conservant une masse réduite. Néanmoins, l'utilisation de ces alliages nécessite une attention particulière quant à la protection contre la corrosion, notamment par l'application de traitements de surface adaptés tels que l'anodisation ou l'alodine.
Les alliages de titane, tels que le Ti-6Al-4V, représentent une alternative haut de gamme pour les applications aéronautiques les plus exigeantes. Cet alliage α+β offre une résistance spécifique exceptionnelle, avec une résistance à la traction pouvant dépasser 900 MPa pour une densité de seulement 4,43 g/cm³. La résistance naturelle à la corrosion du titane, due à la formation spontanée d'une couche d'oxyde protectrice, constitue un avantage majeur dans les environnements agressifs rencontrés en aéronautique. Les clavettes en Ti-6Al-4V trouvent leur place dans les assemblages critiques soumis à des contraintes thermiques et mécaniques élevées, tels que les systèmes de transmission de puissance des moteurs d'avions.
L'intégration de ces alliages légers dans la conception des clavettes aéronautiques s'accompagne de défis technologiques spécifiques. La différence de dureté entre ces matériaux et les aciers traditionnellement utilisés pour les arbres et moyeux nécessite une optimisation des géométries et des tolérances d'ajustement pour prévenir l'usure prématurée des surfaces de contact. De plus, la sensibilité de certains alliages d'aluminium à la corrosion galvanique impose l'adoption de mesures préventives, telles que l'utilisation de revêtements isolants ou l'insertion d'éléments sacrificiels, pour garantir l'intégrité à long terme des assemblages en environnement aéronautique.
L'évolution constante des alliages légers pour applications aéronautiques ouvre de nouvelles perspectives dans la conception des clavettes haute performance. Les recherches actuelles se concentrent sur le développement d'alliages d'aluminium-lithium et de composites à matrice métallique, visant à repousser encore les limites en termes de rapport résistance/poids. Ces avancées matérielles, couplées à des techniques de fabrication additive en plein essor, laissent entrevoir la possibilité de créer des clavettes aux géométries optimisées et aux propriétés mécaniques adaptatives, répondant ainsi aux exigences toujours plus strictes de l'industrie aérospatiale en matière de performance et de fiabilité.
Tolérances géométriques requises pour un ajustement parfait
La précision dimensionnelle et géométrique des clavettes joue un rôle déterminant dans la qualité et la fiabilité des assemblages mécaniques. Les tolérances géométriques définissent les écarts admissibles par rapport aux formes théoriques parfaites, assurant ainsi un ajustement optimal entre la clavette, l'arbre et le moyeu. Cette maîtrise des tolérances impacte directement la répartition des contraintes, la stabilité de l'assemblage et sa durée de vie. L'établissement de spécifications géométriques appropriées nécessite une compréhension approfondie des interactions mécaniques et des conditions de fonctionnement de l'ensemble.
La norme ISO 2768 fournit un cadre de référence pour la définition des tolérances générales applicables aux clavettes. Cependant, pour les applications critiques, des tolérances plus serrées peuvent être spécifiées. La planéité des faces latérales de la clavette, par exemple, influence directement la qualité du contact avec les rainures de l'arbre et du moyeu. Une tolérance de planéité de l'ordre de 0,01 mm pour 100 mm de longueur assure une répartition uniforme des efforts et minimise les risques de concentration de contraintes. La rectitude des arêtes longitudinales de la clavette, quant à elle, garantit un alignement précis dans la rainure, évitant ainsi les phénomènes de coincement ou de jeu excessif.
Le parallélisme entre les faces supérieure et inférieure de la clavette revêt une importance particulière pour assurer une transmission homogène du couple. Une tolérance de parallélisme de 0,02 mm sur la longueur totale de la clavette permet de maintenir un contact uniforme avec l'arbre et le moyeu, réduisant ainsi les risques d'usure localisée et de défaillance prématurée. La perpendicularité des faces d'extrémité par rapport à l'axe longitudinal de la clavette contribue à une répartition équilibrée des contraintes de cisaillement. Une tolérance de perpendicularité de 0,05 mm s'avère généralement suffisante pour garantir un fonctionnement optimal de l'assemblage. Le tabteau ci-dessous présente les caractéristiques géométriques :
Caractéristique géométrique | Tolérance typique | Impact sur la performance |
---|---|---|
Planéité des faces latérales | 0,01 mm / 100 mm | Répartition uniforme des efforts |
Rectitude des arêtes longitudinales | 0,03 mm sur la longueur totale | Alignement précis dans la rainure |
Parallélisme faces supérieure/inférieure | 0,02 mm sur la longueur totale | Transmission homogène du couple |
Perpendicularité des faces d'extrémité | 0,05 mm | Répartition équilibrée des contraintes de cisaillement |
La maîtrise des tolérances dimensionnelles s'avère tout aussi cruciale que celle des tolérances géométriques. La largeur de la clavette, en particulier, détermine la qualité de l'ajustement dans la rainure. Une tolérance h9 sur la largeur assure un ajustement glissant précis, facilitant le montage tout en limitant le jeu fonctionnel. La hauteur de la clavette, quant à elle, influence directement la profondeur d'engagement dans l'arbre et le moyeu. Une tolérance h11 sur la hauteur offre un compromis satisfaisant entre facilité de montage et précision d'ajustement. Ces spécifications dimensionnelles, combinées aux tolérances géométriques, garantissent un assemblage stable et durable.
L'obtention de ces tolérances serrées nécessite la mise en œuvre de procédés de fabrication de haute précision. L'usinage par électroérosion à fil (EDM) s'impose comme une technique de choix pour la réalisation de clavettes aux géométries complexes et aux tolérances exigeantes. Ce procédé permet d'atteindre des précisions de l'ordre du micron, tout en assurant une excellente qualité de surface. Pour les productions en grande série, le rectifiage de précision offre une alternative économiquement viable, capable de maintenir des tolérances serrées sur des volumes importants. La mise en place de contrôles dimensionnels rigoureux, utilisant des techniques de métrologie avancées telles que la tomographie computerisée ou la profilométrie laser, garantit la conformité des clavettes aux spécifications les plus strictes.
Méthodes de fixation des clavettes les plus fiables
La sécurisation des clavettes au sein des assemblages mécaniques constitue un aspect critique de leur conception et de leur mise en œuvre. Les méthodes de fixation employées doivent non seulement assurer un maintien robuste de la clavette dans sa position fonctionnelle, mais également permettre un démontage aisé pour les opérations de maintenance. Le choix de la technique de fixation dépend de multiples facteurs, incluant les conditions de fonctionnement, les contraintes environnementales et les exigences de fiabilité spécifiques à l'application.
La fixation par vis de pression représente une méthode largement répandue pour la sécurisation des clavettes dans les assemblages d'arbres et de moyeux. Cette technique consiste à insérer une vis à travers le moyeu, perpendiculairement à la clavette, exerçant ainsi une pression directe sur celle-ci. L'utilisation de vis à tête creuse hexagonale (CHC) en acier haute résistance, conformes à la norme ISO 4762, assure une excellente tenue mécanique. Le couple de serrage de ces vis doit être soigneusement contrôlé pour éviter toute déformation de la clavette ou du moyeu. Un couple typique de 10 à 15 N.m pour une vis M6 offre généralement un compromis satisfaisant entre force de maintien et préservation de l'intégrité des composants. L'ajout d'un frein-filet anaérobie de classe moyenne, tel que le Loctite 243, renforce la résistance au desserrage sous vibrations, garantissant ainsi la stabilité à long terme de l'assemblage.
Pour les applications soumises à des contraintes dynamiques importantes, la fixation par goupille élastique constitue une alternative robuste. Cette méthode implique l'insertion d'une goupille cylindrique fendue, généralement en acier à ressort, dans un alésage traversant simultanément l'arbre et la clavette. Les goupilles élastiques normalisées selon la norme ISO 8752 offrent une excellente résistance au cisaillement et à la fatigue. Le dimensionnement de la goupille doit prendre en compte les efforts de cisaillement maximum auxquels l'assemblage sera soumis. Une goupille de diamètre équivalent à 25% de la largeur de la clavette assure généralement une tenue mécanique optimale. L'insertion de la goupille nécessite un outillage spécifique pour éviter toute déformation lors du montage, garantissant ainsi un ajustement serré et durable.
Les assemblages nécessitant une sécurisation maximale peuvent bénéficier de techniques de fixation combinées. L'association d'une vis de pression avec une goupille transversale offre une redondance de maintien, particulièrement adaptée aux applications critiques où la défaillance de la clavette pourrait entraîner des conséquences graves. Dans ce cas, la vis de pression assure le positionnement axial précis de la clavette, tandis que la goupille prévient tout mouvement radial. Cette configuration hybride nécessite une conception soignée de l'interface arbre-moyeu pour accommoder les deux éléments de fixation sans compromettre l'intégrité structurelle de l'ensemble. L'utilisation de matériaux compatibles pour la vis, la goupille et les composants principaux s'avère cruciale pour prévenir les phénomènes de corrosion galvanique susceptibles d'affaiblir la liaison mécanique au fil du temps.